This design example illustrates the evolution of a real-time embedded supervisory control and data acquisition (SCADA) system from proof-of-concept (PoC) to validated system. TCB Engineers worked closely with the customer to identify critical to quality requirements (CTQs) and utilized a disciplined Systems Engineering approach to realize the final system.
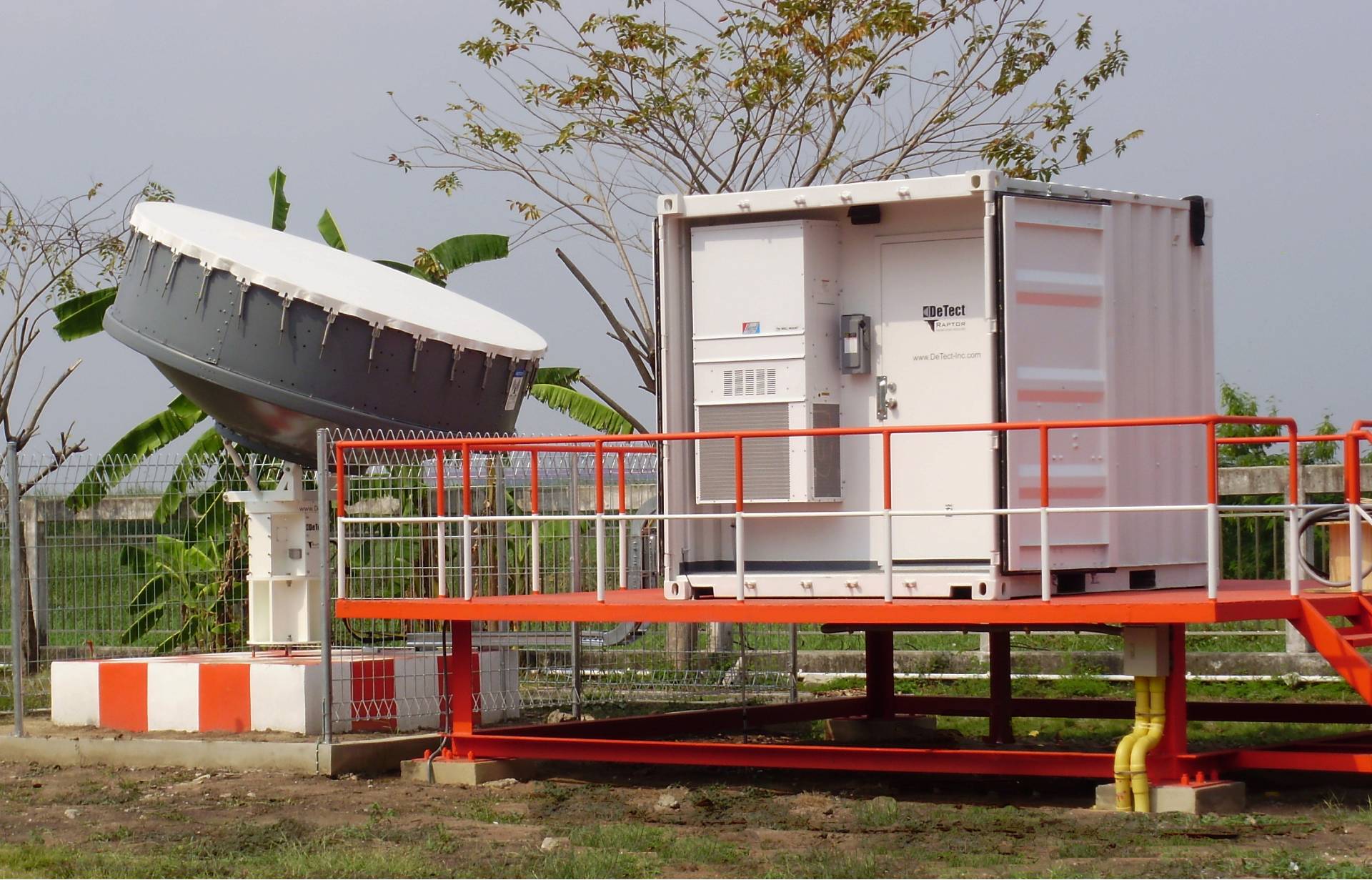
The Challenge
A RADAR OEM needed a safety controller capable of detecting and reacting to adverse conditions within a few micro-seconds. The controller would need to monitor a mix of ~150 analog and digital channels with both high speed and high accuracy, and maintain reliable operation in the presence of nearby kilowatt-class RF transmitters. Success of the project would be measured by the ability to accomplish this task while remaining immune to false triggering in the adverse electromagnetic environment of a RADAR shack.
High Reliability SCADA
Design of high reliability systems for harsh environments demands a solid understanding of signals & systems in order to be successful. In this case, two reliability contributors dominated the solution path:
Measurement Reliability in the form of repeatability and accuracy of measured parameters.
System Reliability as the ability to maintain operation in the presence of adverse conditions, including EMI.
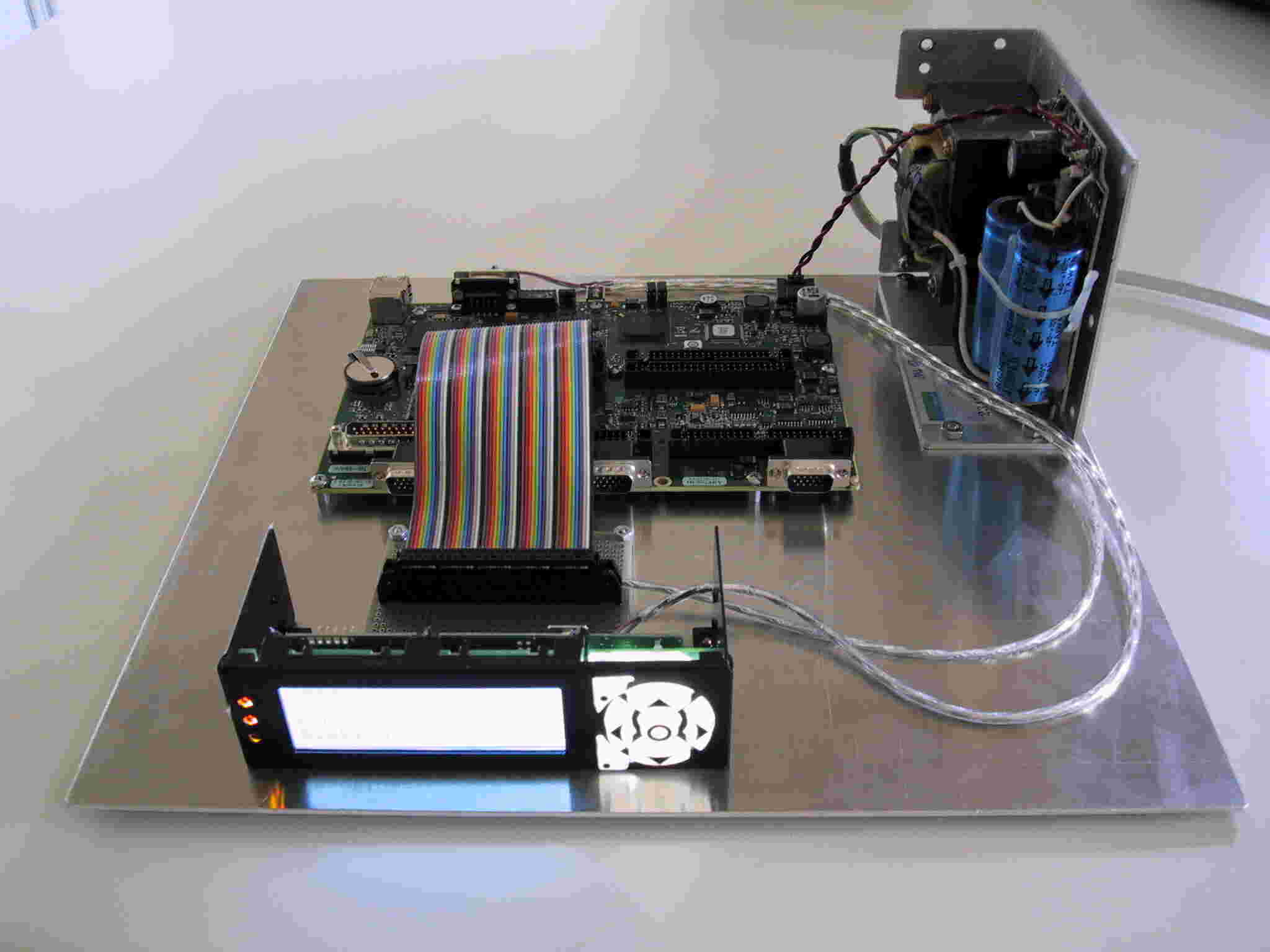
Phase I - Proof-of-Concept
TCB Engineers chose a National Instruments sbRIO embedded controller as a basis for the design, due in part to compact form factor and real-time operating system. The potential for high voltage and/or high levels of electromagnetic interference (EMI) precluded the use of a commercial off-the-shelf (COTS) sbRIO mezzanine board. Designing a custom mezzanine printed circuit board accommodated these requirements and afforded I/O expansion beyond conventional limits.
Software Solution
The sbRIO FPGA provides a high-speed, deterministic platform to host critical safety functionality, while the ARM side provides familiar access to administrative functionality. Extensive reporting of system parameters is provided to a centralized controller not part of this subsystem. Configuration and administration are facilitated either via central controller push, a browser-based user interface, or front panel LCD controls.
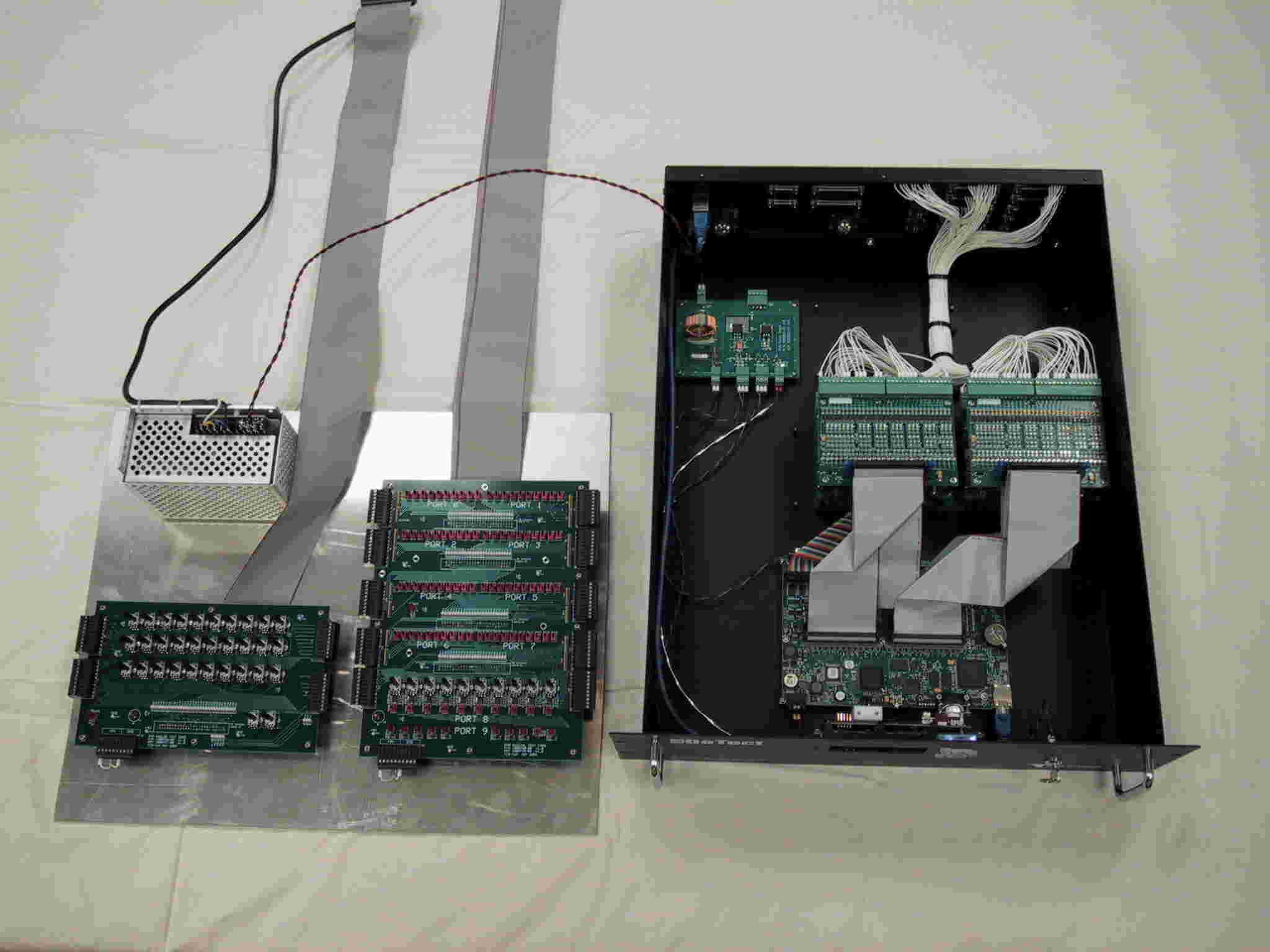
Phase II - Validation Prototype
A validation prototype was constructed to vet the implementation approach, including custom electronic assemblies for signal conditioning and power conversion. Packaging consisted of a custom 3U rack chassis, which afforded ample space in which to house the various assemblies.
A set of I/O simulators were developed to enable stand-alone channel scenario testing. The simulators doubled as a development platform for the embedded software effort and proved especially useful for subsystem and system validation activities later in the program.
System Hardening & Productization
With a vetted proof-of-concept, the task of productization could proceed with certainty. For the hardware, this included designing a robust power supply, optimizing the filter & scaling circuits for each of the ~150 signal inputs, and developing a packaging concept that maximized electromagnetic immunity. Design for manufacturability (DFM) and LEAN concepts were incorporated into the final electrical and mechanical designs, which further reduced complexity and total cost.
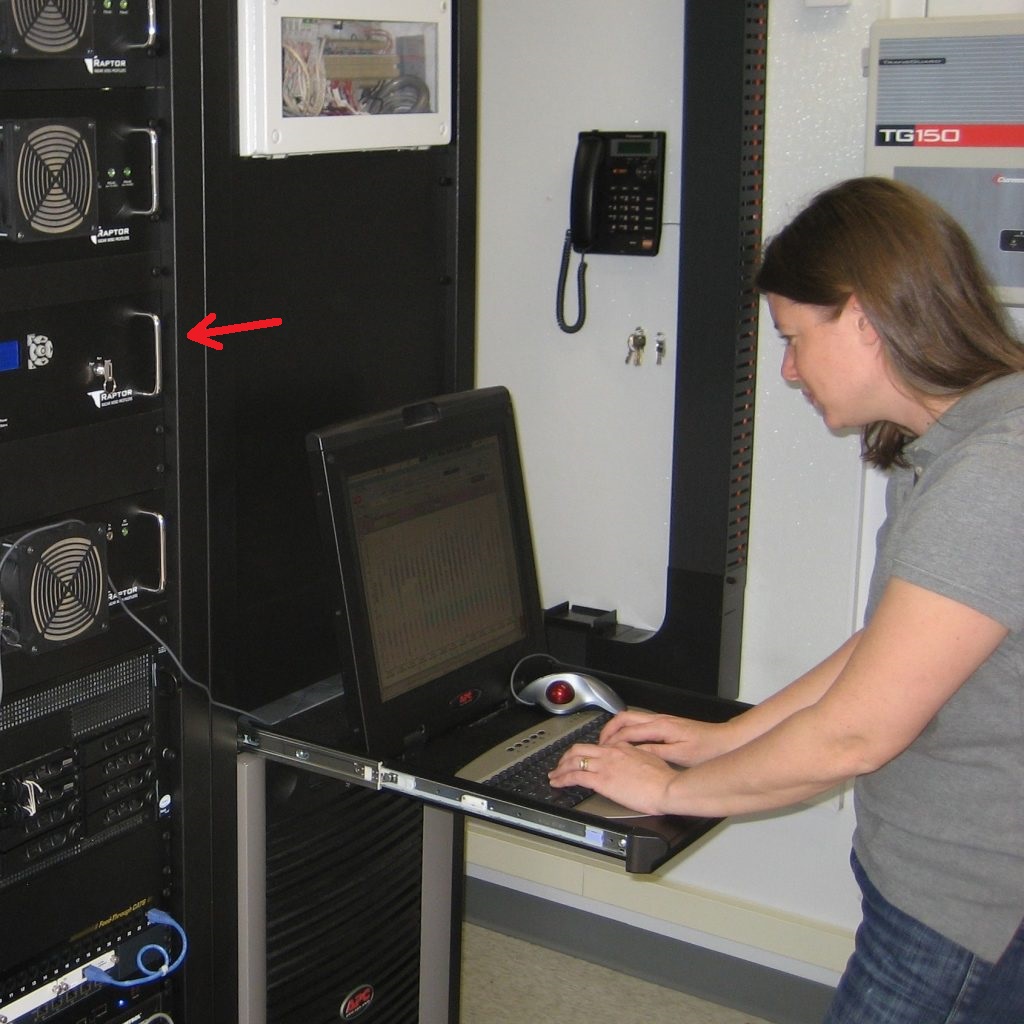
Phase III - System Validation
Several production prototypes were constructed to vet the implementation approach and subjected to various verification and validation (V&V) activities. The simulators doubled as a platform for further software development and proved especially useful for validating upstream reporting infrastructure.
Sustaining Engineering
The system has been in production for several years and has proven to be reliable and sustainable. The approach enabled our customer to capitalize on their ability to maintain the system and a vertical market position, thus demonstrating TCB Engineers’ unique ability to provide complete solutions to complex problems.