This design example illustrates the development evolution of a unmanned aerial vehicle (UAV) payload from proof-of-concept (PoC) to validated system. TCB Engineers worked closely with the customer to identify critical to quality requirements (CTQs) and utilized a disciplined Systems Engineering approach to realize the final system.
Martinez, B.; Miller, T.W.; Yalin, A.P. Cavity Ring-Down Methane Sensor for Small Unmanned Aerial Systems. Sensors 2020, 20, 454. https://doi.org/10.3390/s20020454
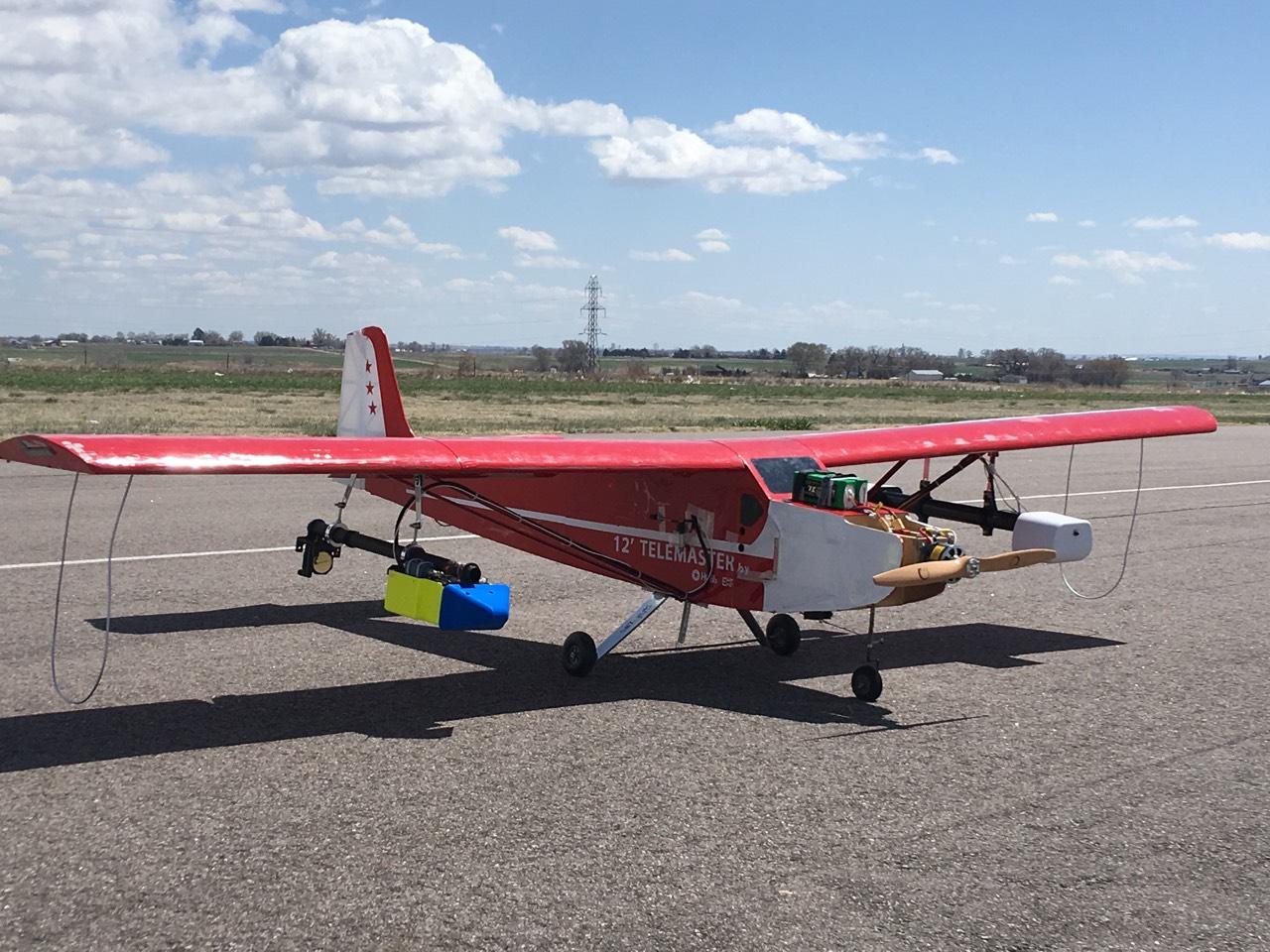
The Challenge
An academic institution needed early-phase NPI assistance with an emerging Cavity Ringdown Spectroscopy (CRDS) trace gas sensor technology that was the subject of pure research. Success of the project would be measured by the ability to demonstrate working sensors in geographically disparate portable, vehicle and Unmanned Aerial Vehicle (UAV) applications. Key metrics of success are integration at the scale of size weight and power (SWaP) dictated by the application, and utilization of internet of things (IoT) techniques to remotely publish data in real time.
High Reliability & Extreme SWaP
Design of high reliability UAV payloads demands an systems approach to balance competing goals:
SWaP in the form of designing compact, efficient and robust circuits that tightly integrate with an optimized mechanical design.
System Reliability as the ability to maintain operation in the presence of adverse conditions, including vibration and extreme temperatures.
System Survivability as the ability to resume operation after extreme events, such as power fluctuation or hard landing.
TCB Engineers specified the National Instruments sbRIO-9651 Single Board RIO system-on-module (SOM) as the embedded controller primarily due to advantageous size, weight and power (SWaP) vs. computational capability, but also because the customer was already familiar with the LabVIEW RT-FPGA development system. The sbRIO-9651 is based on the Xilinx Zync-7000 system-on-chip (SoC), a diverse product family that integrates a ARM Cortex-A9 CPU, FPGA and several peripherals on a single integrated circuit.
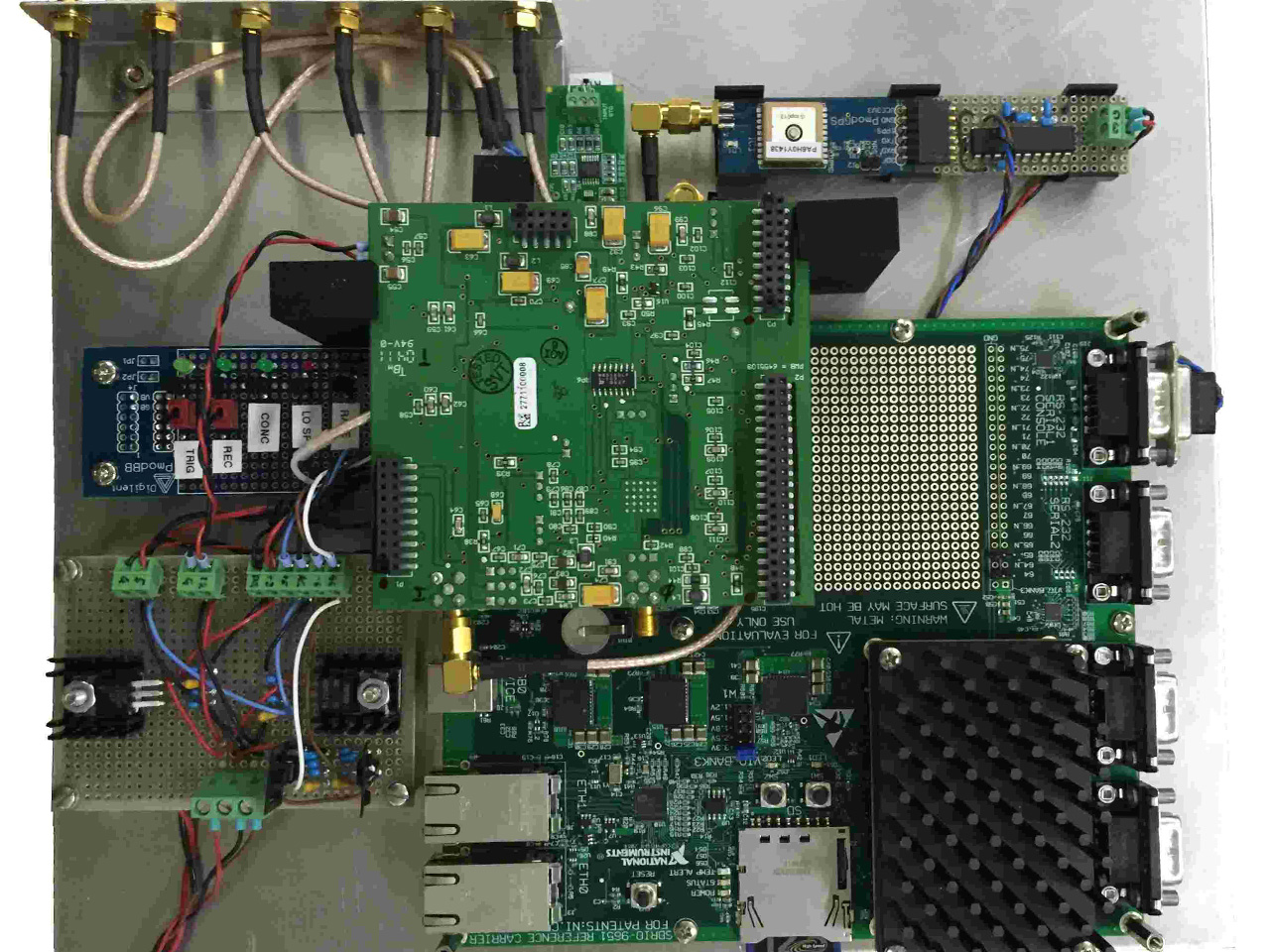
Phase I - Proof-of-Concept
A detailed systems design was performed and critical components were selected, including the sbRIO-9651 SOM from National Instruments. Evaluation boards from silicon vendors were integrated where available and various prototyping methods were utilized for those that were not. The prototype was substituted into the academic system for comparison and results were highly favorable with a SWaP reduction of 90%.
Software Solution
The sbRIO FPGA provides the high-speed, deterministic platform necessary for signal acquisition and processing, while the ARM side provides access to administrative functionality. LabVIEW embedded Realtime and FPGA software were developed to implement CTQs. Store-and-forward techniques were implemented to guarantee losses transfer of raw data to an AWS-based analytics platform, where it can be formatted and disseminated.
Phase II - Portable Validation Prototype
Electronics from the previous phase were augmented with a custom in-house power supply PCBA to facilitate compliance with SAE standards. A cellular gateway was integrated to provide remote access. Packaging consisted of a modified NEMA IP67 enclosure, custom heatsink, and vehicle mounting system.
Validation Testing
Thermal chamber testing was performed to verify reliable operation over -20 to +70C ambient and several thousand drive miles were logged with this assembly. The system proved reliable, repeatable and accurate, allowing the customer to focus on complementary project contributions and further SWaP reductions through ancillary component optimization.
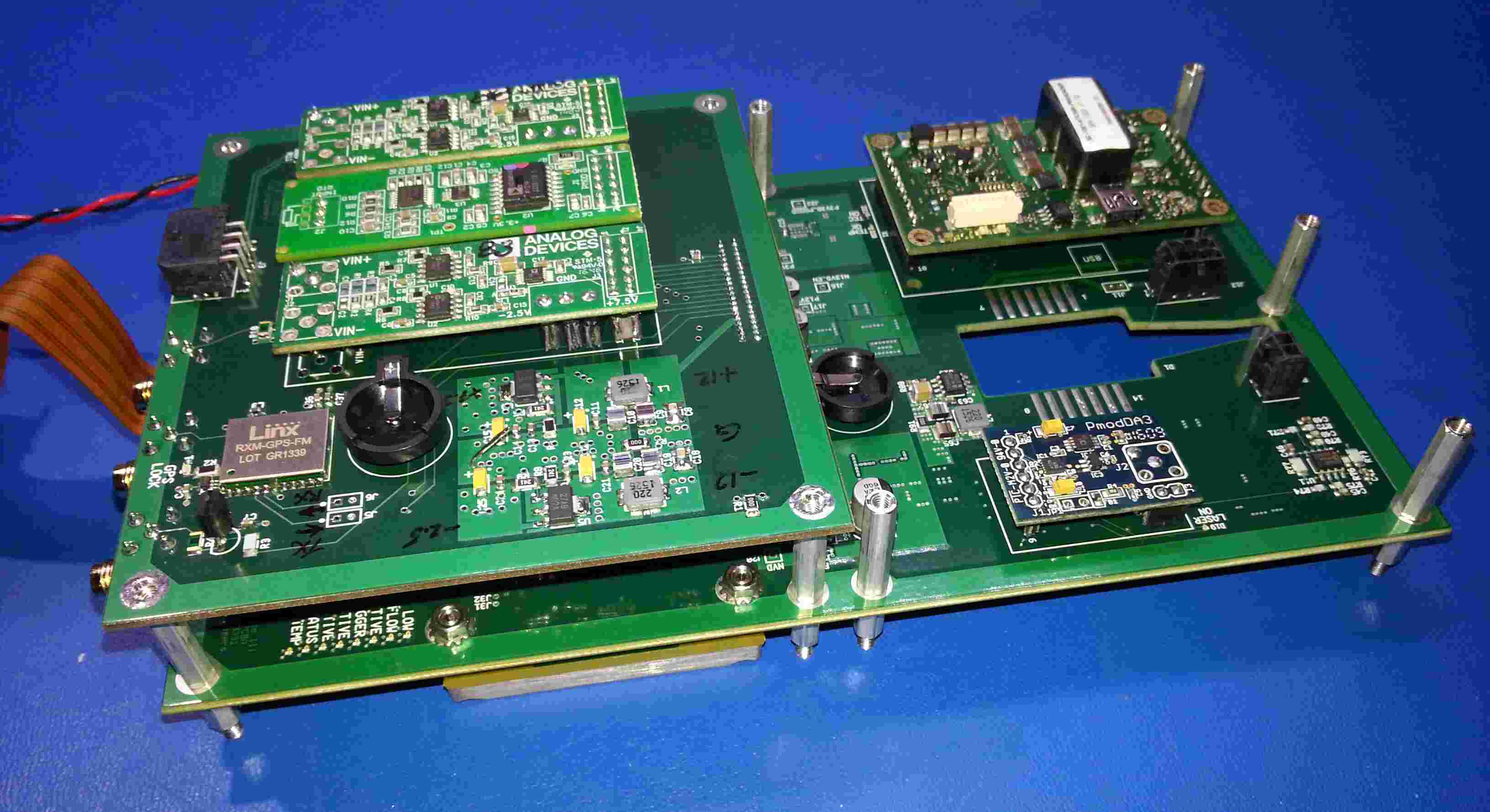
Phase III – SWaP Optimized UAV Payload
Electronics from the previous phase were tightly integrated by designing custom PCBAs, one for power supply & digital, and the other for low noise analog conditioning and sampling. The assembly also includes an on-board DFB laser with its associated thermoelectric (TEC) controller and precision programmable current source.
Packaging
The board stack was housed in a custom carbon fiber enclosure with IP67 sealing. An integrated thermal approach was necessitated by the SWaP requirements, which demanded design coordination between the electrical and mechanical teams. The validation prototype measured approximately 10″L x 6″W x 3″H and weighs about three pounds.
Phase IV - System Validation
Several copies were made and used in various configurations, including fixed operation in the research laboratory, mounted underwing on a UAV, as a drone payload, and on the roof of a test vehicle. This flexibility facilitates a multi-modal approach to trace gas detection and serves as a platform to advance the growing field fugitive emissions quantification.
Field Deployment
The system has been successfully deployed in a wide range of settings, including Texas summers and Wyoming winters with highly repeatable results. Verified accuracy and repeatability of single-digit part-per-million was achieved across a wide temperature range, affording accurate measurement in outdoor applications. This system enabled further research and proved to be an important contributor to the maturation of oil and gas well emissions monitoring technology.